Wie wird Messing hergestellt?
Der Werkstoff Messing kann auf eine lange Geschichte zurückblicken – antike Kulturen waren mit der Messingherstellung und dem Mischungsverhältnis der Legierung– zwei Drittel Kupfer und ein Drittel Zink – bereits vor mehreren Jahrtausenden vertraut.
Während man seinerzeit Kupfer schon längst in größerem Maßstab gewinnen konnte, sah es mit der Verfügbarkeit von Zink gänzlich anders aus. Das Metall ließ sich nämlich weder ohne Weiteres herstellen, noch wusste man, dass Zink als solches existiert. Dementsprechend war auch die Messingherstellungeine noch völlig andere, als wir sie heute kennen.
Heute ohne Bedeutung mehr: Das Galmei-Verfahren
Eine antiquierte und bis Mitte des 18. Jahrhunderts sogar nur die einzige angewandte Methode ist uns heute als „Messingbrennen“ oder „Galmei-Verfahren“ bekannt. Der Name dieser Methode lässt sich auf den Legierungszusatz Galmei zurückführen – einem Zinkerz, von welchem man für lange Zeit nicht wusste, dass er überhaupt Zink enthält.
Zur Messingherstellung wurde der Galmei zunächst gemahlen, mit gemahlener Holzkohle vermischt und anschließend im Verhältnis von 2:1 mit Kupferstücken in einem Schmelztiegel auf bis etwa 1.000 °C erhitzt. Bei diesen Prozesstemperaturen, die bei der sogenannten Reduktion mit Kohlenstoff benötigt werden, wird der Siedepunkt des enthaltenen Zinks überschritten und das Metall verdampft – ein Grund, weshalb Zink lange Zeit unentdeckt blieb.
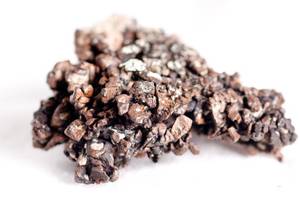
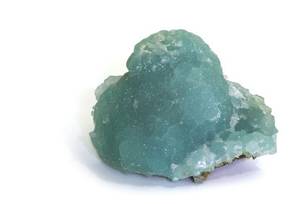
Denn die heißen Zinkdämpfe lösen das enthaltene Kupfer an und bilden so direkt eine Messinglegierung, ohne dass es dabei je in flüssiger Form sichtbar wird. Folglich war es auch nicht bekannt, dass bei diesem Vorgang eine Legierung aus zwei Metallen entsteht. Man hielt Galmei stattdessen für ein farbgebendes Mineral – und Messing schlichtweg als goldgelb gefärbtes Kupfer.
Vom Kunsthandwerk zur Massenproduktion
Doch nicht nur die Herstellung und Wahrnehmung von Messing war in der Vergangenheit eine andere, sondern auch die Verwendung des Metalls. Man nutzte es unter anderem im Römischen Reich zur Anfertigung von Münzen, vor allem aber wurden seit dem Hochmittelalter zahlreiche künstlerische Gegenstände daraus gefertigt.
Mit der Entstehung der Zink-Destillierhütte und der industriellen Messingproduktion gegen Ende des 18. Jahrhunderts verlor das Galmeiverfahren schließlich an Bedeutung. Denn nicht nur die Produktionskosten konnten durch das Zink-Destillationsverfahren deutlich gesenkt werden, auch standen im Zuge der Industrialisierung neue Verfahren und Maschinen zum wirtschaftlichen Schmieden, Gießen, Ziehen und Walzen von Messing-Halbzeugen zur Verfügung, zum Beispiel:
Von nun an konnten diese und viele andere Messingprodukte schnell und in hohen Stückzahlen gefertigt werden. Heute sind sie in allen erdenklichen Industrien und Branchen unverzichtbar.
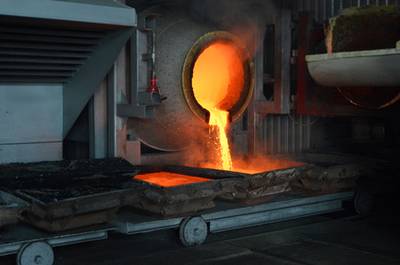
Die Herstellung von Messing im Wandel
Für eine möglichst effiziente Messingherstellung wie wir sie heute kennen, sind – von der Schmelze bis zum weiterverarbeitungsgerechten Endprodukt – durchgängige, sprich: kontinuierliche Fertigungsprozesse nötig. Darauf sind die Hersteller heutzutage in der Regel eingestellt und verwenden für ein bestmögliches Resultat entsprechend hochwertige Grundmaterialien, zum Beispiel in Form von reinen Metallen und Vorlegierungen.
Allerdings werden häufig auch Schrotte zur Messingherstellung genutzt und die Recyclingrate liegt hier bei mehr als 90 Prozent. Zurecht, denn beim Wieder-Einschmelzen und Recycling von Messingschrott sind keinerlei Verluste in puncto Qualität zu erwarten. Auf diese Weise können immer wieder qualitativ hochwertige Produkte aus ihnen entstehen – ein Vorteil, der heute gerne ausgeschöpft wird.
Generell hat sich das Schmelzen und Gießen im Laufe der Zeit stark weiterentwickelt. Arbeitete man bis in die 1920er noch mit koks-, öl- oder gasbefeuerten Anlagen, so lösten wesentlich leistungsfähigere, elektrische Induktions-Rinnenofen diese ab. Der Herstellungsprozess selbst blieb allerdings noch diskontinuierlich. Rund 30 Jahre später setzte sich das Stranggießverfahren durch, bei dem das Messing im Ausmaß der Erstarrung fortwährend aus der Form gezogen wird. Erst ab 1960 begann schließlich die kontinuierliche Fertigung in Anlagen für das Senkrechtstranggießen und auch die Induktionsöfen wurden effizienter und leistungsfähiger.
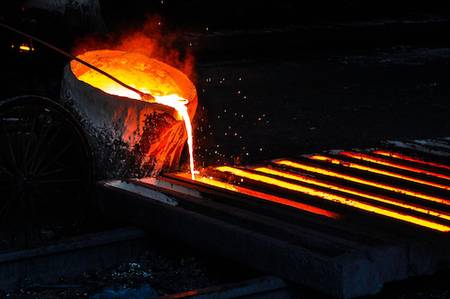
Fortschrittliche Technologie für höchste Messing-Qualität
Heute gelten in Messinggießereien hochtechnische Standards. Man greift auf sehr universelle, automatisiert arbeitenden Schmelz- und Gießanlagen zurück, welche dazu in der Lage sind, Messing im Blockformat vollkontinuierlich herzustellen, die im Anschluss der Fertigung warmverformt werden. Zugleich stehen Anlagen zum Gießen von Messingband und -draht zur nachfolgenden Kaltverformung bereit, während für Messing-Rundbolzen horizontal ausfördernde Stranggießanlagen genutzt werden.
Für diese folgt in der nächsten Verarbeitungsstufe das Warmverformen. Der in einem Schritt stattfindende Vorgang sorgt dafür, dass der Messing-Gussblock den gewünschten Endabmessungen des Halbzeugs nahekommt und weitere Kaltverformungsmaßnahmen auf ein Minimum reduziert werden. Der hohe Verformungsgrad wirkt sich positiv auf die mechanischen Eigenschaften des Messings aus, denn das grobe Gussgefüge wird noch einmal sorgfältig verknetet.
Hierbei kommen neben Blockwalzwerken vorwiegend hydraulische Strangpressen zum Einsatz. Die gegossenen Messingblöcke werden aus einer Druckkammer mithilfe eines Stempels durch eine Werkzeugöffnung gepresst. Die Querschnitte letzterer können von kreisrund bis hin zu verwinkelten Formen mit Hohlräumen variieren. Somit lassen sich auch sehr dünnwandige Messingrohre durch das Strangpressverfahren herstellen.
Das Messing ist nach dem Strangpressen noch relativ weich. Um höhere Verfestigungsgrade zu erreichen, sind deshalb mehrere Kaltformschritte nötig. Zudem sollen dem Kaltverformen die gewünschten Endabmessungen aber auch mechanischen Eigenschaften möglichst genau erreicht werden. Das warmgewalzte Messingband wird zunächst mit Walzen großen Durchmessers und anschließend mit kleineren Walzen auf das Zielmaß gebracht.
Nicht bei allen Messingsorten sorgt das Strangpressen oder Warmwalzen dafür, dass die geforderten Endabmessungen erreicht werden, weshalb Zwischenglühungen in Durchlauföfen durchgeführt werden müssen. Zerspanungsmessinge zeichnen sich positiverweise dadurch aus, dass sie sich immer bis nahe an die Endabmessungen strangpressen lassen. Sie müssen daher nur noch ein Mal durch das Ziehen kaltverformt werden, um auch die geforderten, engen Toleranzen zur Weiterverarbeitung auf Hochleistungsautomaten zu gewährleisten.