Laserschweißen
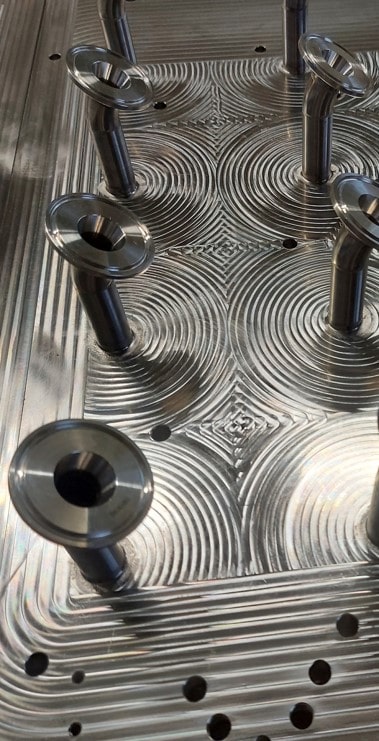
Es ist zweifellos eines der am technologisch fortschrittlichsten Schweißverfahren, um verschiedenste Werkstoffe hochpräzise miteinander zu verbinden – die Rede ist vom Laserschweißen. Es eignet sich hervorragend dazu Materialien wie Edelstahl, Kupfer, Titan und Aluminium zu fügen. Mit dem Laserschweißen können auch Mischverbindungen wie Aluminium-Kupferverbindung oder Edelstahl-Kupferverbindung realisiert werden. Dank seiner hohen Automatisierbarkeit und vieler weiterer Vorteile (unten aufgeführt) ist das Verfahren in etlichen Bereichen der Industrie zunehmend etabliert.
Optimale Bedingungen für Laserschweißen
Zunächst ist Laserschweißen ideal, wenn sehr enge Toleranzen realisiert werden müssen. Der Herstellungsprozess bietet eine exakte Steuerung des Schweißprozesses, was zu hochpräzise Laserschweiß-Verbindungen führt und eine dauerhafte Reproduzierbarkeit garantiert. Ebenfalls ist das Laserschweißen für das Schweißen von dünnen Materialien geeignet, da die Hitze lokalisiert ist und die Gefahr von Verzug oder Material Durchbrennen so gut wie ausgeschlossen ist. Insgesamt wird das Laserschweißen empfohlen, wenn Präzision, Geschwindigkeit und Materialschutz im Vordergrund stehen.
Müssen äußerst umfangreiche, komplexe Geometrien und schwer zugängliche Stellen per Laserschweißen bearbeitet werden, greifen wir auf unsere 8-Achsen-Robotersysteme mit zusätzlicher Dreh-Kipp Tisch Funktion zurück. Hier sind Schweißbereiche von 4.000 x 2.000 x 1.500 mm und D 1.500 x 2.000 mm möglich. Auf Anfrage realisieren wir auch größere Dimensionen. Bei zu großen Bauteilen bieten wir auch mobiles Laserschweißen bei Ihnen vor Ort an. Dank 20 Jahre Erfahrungen und fundiertes Experten-Knowhow in der Laserschweißtechnik verstehen wir uns als Partner für jeden Auftrag von der Grundlagenentwicklung über die Fertigung von Prototypen bis hin zur Serienproduktion.
Vorteile des Laserschweißens: Präzision und Effizienz
- Keine Schweißnahtvorbereitung – Im Laserschweißen wird Stoß auf Stoß geschweißt.
- Keine Nacharbeit der Schweißnähte notwendig – Mit dem Laser können die Nähte geglättet werden.
- Materialvielfalt – Es können etliche Werkstoffe gefügt werden. Auch Mischverbindungen sind möglich.
- Hohe Schweißqualität – Wir erreichen bis zu 10 mm Schweißtiefen, schmale und gleichmäßige Nähte mit hoher Festigkeit und Dichtheit
- Geringer Wärmeeintrag – Im Vergleich zu den herkömmlichen Schweißverfahren verursacht das Laserschweißen nur einen geringen Energieeintrag. Schlussfolgernd resultiert daraus eine begrenzte Wärmeeinflusszone und kaum thermischer Verzug.
- Wiederholgenauigkeit – Hoher Automatisierungsgrad gewährleistet eine konstante Qualität in der Serienproduktion
- Nahtgeometrie – Wir erreichen schlanke Schweißnähte
- Hohe Schweißgeschwindigkeit – Durch die schnelle Erwärmung und das effiziente Schmelzen können kurze Verarbeitungszeiten erreicht werden.
Technologie des Laserschweißens
Das Laserschweißen basiert auf der Nutzung eines hochenergetischen Laserstrahls, der präzise auf die Schweißstelle fokussiert wird. Die hohe Energiedichte des Lasers ermöglicht es, das Material schnell zu schmelzen und eine hochfeste Verbindung zu erzeugen. Dabei verwenden wir unterschiedliche Laserarten, wie Faserlaser, CO2-Laser und Hybridlaser, je nach den spezifischen Anforderungen des Materials und der Anwendung.
Grenzen des Laserschweißens: Die Alternativen
In gesonderten Fällen, in denen Laserschweißen nicht geeignet ist, bieten wir das Löten, MIG/MAG-Schweißen oder das Elektronenstrahlschweißen als effektive Alternative zum Laserschweißen an. Diese Verfahren werden je nach Projektanforderungen ausgewählt. Müssen präzise sowie temperatursensitive Bauteile miteinander verbunden werden, greifen wir intern auf das Löten zurück. Werden dickere Materialien bis zu 20 mm miteinander verbunden nutzen wir das MIG/MAG-Schweißen oder das Elektronenstrahlschweißen (EB-Schweißen)