Aluminiumlegierungen für den Schiffbau
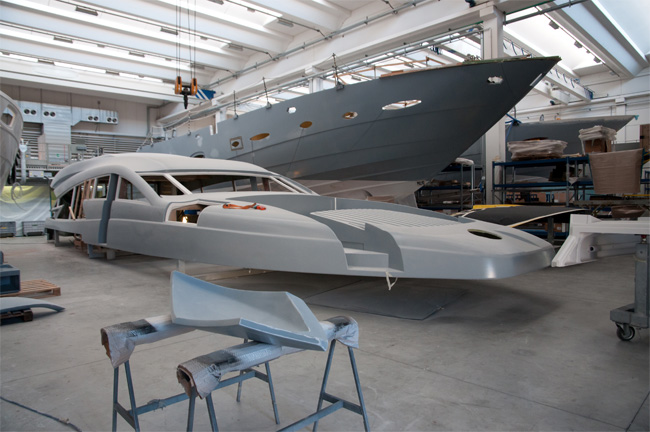
Was sie aushalten müssen und welche die richtigen sind
Stürmische See. Aus Meeresrauschen wird ohrenbetäubendes Getöse. Unermüdlich schlagen die Wellen ans Schiff und die Gischt peitscht weit über das Deck. Normaler Alltag auf hoher See. Doch auch, wenn es gerade mal nicht stürmisch ist, sind Schiffe permanent mit Salzwasser oder salzhaltiger Luft, aber auch mit See-, Brack- oder Hafenwasser in Kontakt. Selbstredend, dass im Schiffbau nicht jeder beliebige Werkstoff verwendet werden kann. Hier ist neben vielen anderen Materialien auch meerwasserbeständiges Aluminium gefragt, das klaren Anforderungen genügen muss. Wissen Sie schon, welche Aluminiumlegierung für Ihre Anwendung im Schiffbau die Richtige ist? Im Folgenden haben wir Ihnen ein paar Informationen dazu zusammengestellt.
Was heißt eigentlich „meerwasserbeständig“?
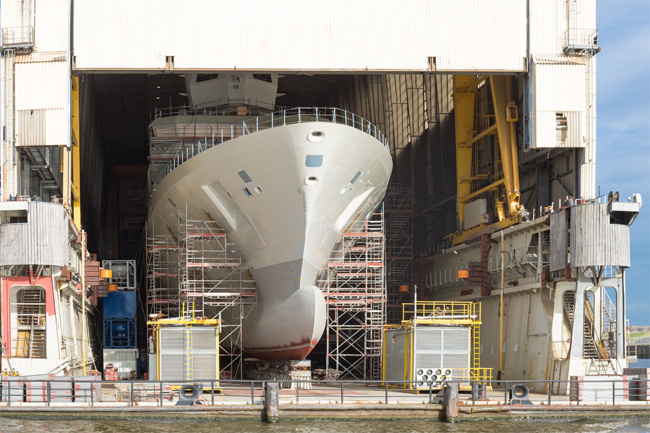
Dass Aluminium im Schiffbau vor allem wegen seines geringen Gewichts bei gleichzeitig hoher Stabilität zum Einsatz kommt, liegt auf der Hand. Sie können sich sicherlich vorstellen, dass es in puncto Gesamtgewicht und Energieverbrauch einen großen Unterschied macht, ob man Aluminium-Schiffbauprofile verbaut oder entsprechende Pendants aus Stahl. Erst recht bei Meeresgiganten wie Kreuzfahrt- und Containerschiffen.
Wie eingangs erwähnt wird Aluminiumlegierungen Meerwasserbeständigkeit abverlangt. Aber was bedeutet das eigentlich? Im Schiffbau und in der Meerestechnik steht Meerwasserbeständigkeit für die Werkstoffeigenschaft, dass die Legierung als Konstruktionswerkstoff eingesetzt werden kann, schweißbar ist und ein gutes Korrosionsverhalten gegenüber Meerwasser und in Meerwasseratmosphäre aufzeigt. Beim Germanischen Lloyd und in der in der DIN 81249-1 ist in diesem Zusammenhang von „seewassergeeignet“ die Rede. Unterm Strich bedeutet dies, dass die Legierung keinen Korrosionsschaden innerhalb der geplanten Nutzungsdauer davontragen sollte.
Welche Aluminiumlegierungen sind für den Schiffbau geeignet?
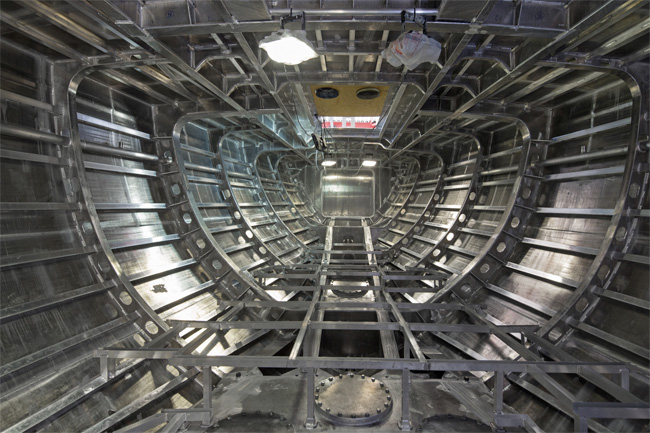
Reines Aluminium ist zwar bereits extrem korrosionsbeständig, doch es wird in der Industrie nur relativ selten eingesetzt. Dies liegt oft daran, dass die benötigten Endprodukte spanend bearbeitet werden müssen – und dafür ist Reinaluminium nicht geeignet. Daher müssen andere Metalle hinzulegiert werden, sowohl um die Bearbeitung zu ermöglichen, als auch die Korrosionsbeständigkeit beizubehalten. Seine hohe Korrosionsbeständigkeit erreicht Aluminium durch Magnesium als Hauptlegierungszusatz. Aluminium-Magnesium-Legierungen (AlMg), die im Schiffbau eingesetzt werden, sind zum Beispiel:
Aluminiumlegierungen dieser Art sind nicht nur widerstandsfähig gegen Salzwasser und Meeresatmosphäre. Ein weiterer Aspekt, der im Schiffbau zum Tragen kommt, ist nämlich der Kontakt von Aluminiumlegierungen mit anderen Materialien. Stichwort: Kontaktkorrosion. In der Regel werden an Bord Aluminiumprofile, Aluminiumdraht, Platten und Bleche sowie Aluminiumstangen & Co. mit verschiedensten Komponenten und Bauteilen aus anderen Werkstoffen verschweißt, verlötet, verschraubt, vernietet oder auf andere Art miteinander in Verbindung gebracht. Sind Aluminiumlegierungen in Konstruktionen mit edleren Metallen wie Eisen oder Kupfer in Kontakt, kann mit sich bei Feuchtigkeitszutritt ein sogenanntes Kontaktelement bilden – eine elektrochemische Reaktion.
Durch Wasser oder Luftfeuchtigkeit als elektrolytischen Leiter fließen hier die Elektronen vom unedleren zum edleren Metall, beispielsweise am Verbindungspunkt zwischen einem Aluminiumprofil und einer Kupferschraube. Innerhalb kurzer Zeit zeigen sich hier und mehrere Millimeter ringsum Korrosionserscheinungen, die eine dauerhaft sichere Verbindung unmöglich machen.